ICE SAS : International Coaching Engineering

TOOL BOX


ABC method
In materials management, the ABC analysis (or Selective Inventory Control) is an inventory categorization technique. ABC analysis divides an inventory into three categories- "A items" with very tight control and accurate records, "B items" with less tightly controlled and good records, and "C items" with the simplest controls possible and minimal records.
MRP II
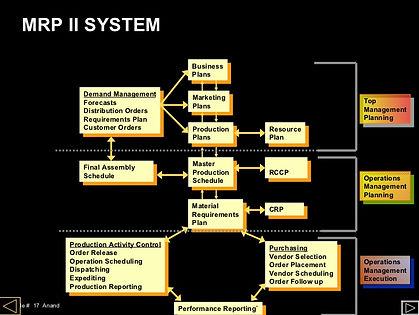
Manufacturing resource planning (MRP II) is defined as a method for the effective planning of all resources of a manufacturing company. Ideally, it addresses operational planning in units, financial planning, and has a simulation capability to answer "what-if" questions and extension of closed-loop MRP.
Benefits
MRP II systems can provide:
-
Better control of inventories
-
Improved scheduling
-
Productive relationships with suppliers
For design / engineering:
-
Improved design control
-
Better quality and quality control
For financial and costing:
-
Reduced working capital for inventory
-
Improved cash flow through quicker deliveries
-
Accurate inventory records


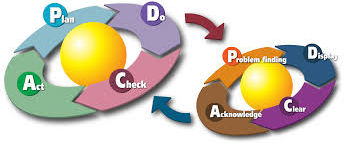

Kanban is one method to achieve JIT.
One key indicator of the success of production scheduling based on demand, pushing, is the ability of the demand-forecast to create such a push. Kanban, by contrast, is part of an approach where the "pull" comes from demand. Re-supply or production is determined according to the actual demand of the customer. In contexts where supply time is lengthy and demand is difficult to forecast, often, the best one can do is to respond quickly to observed demand. This situation is exactly what a kanban system accomplishes, in that it is used as a demand signal that immediately travels through the supply chain. This ensures that intermediate stock held in the supply chain are better managed, and are usually smaller. Where the supply response is not quick enough to meet actual demand fluctuations, thereby causing potential lost sales, stock building may be deemed more appropriate, and is achieved by placing more kanban in the system.
To be effective, kanban must follow strict rules of use. Toyota, for example, has six simple rules, and close monitoring of these rules is a never-ending task, thereby ensuring that the kanban does what is required.
Toyota's Six Rules:
1 - Later process picks up the number of items indicated by the kanban at the earlier process.
2- Earlier process produces items in the quantity and sequence indicated by the kanban.
3- No items are made or transported without a kanban.
4- Always attach a kanban to the goods.
5- Defective products are not sent on to the subsequent process. The result is 100% defect-free goods.
6- Reducing the number of kanban increases the sensitivity.

LEAN
Lean is a systematic method for the elimination of waste ("Muda") within a manufacturing system. Lean also takes into account waste created through overburden ("Muri") and waste created through unevenness in work loads ("Mura"). Working from the perspective of the client who consumes a product or service, "value" is any action or process that a customer would be willing to pay for.
Essentially, lean is centered on making obvious what adds value by reducing everything else. Lean manufacturing is a management philosophy derived mostly from the Toyota Production System (TPS) and identified as "lean" only in the 1990s.
The original seven muda are:
-
Transport (moving products that are not actually required to perform the processing)
-
Inventory (all components, work in process, and finished product not being processed)
-
Motion (people or equipment moving or walking more than is required to perform the processing)
-
Waiting (waiting for the next production step, interruptions of production during shift change)
-
Overproduction (production ahead of demand)
-
Over Processing (resulting from poor tool or product design creating activity)
-
Defects (the effort involved in inspecting for and fixing defects)
KAIZEN
Kaizen (改善?), Chinese and Japanese for "improvement". When used in the business sense and applied to the workplace, kaizen refers to activities that continuously improve all functions and involve all employees from the CEO to the assembly line workers. It also applies to processes, such as purchasing and logistics, that cross organizational boundaries into the supply chain.
It has been applied in healthcare, psychotherapy, life-coaching, government, banking, and other industries.
By improving standardized activities and processes, kaizen aims to eliminate waste.
Kaizen is a daily process, the purpose of which goes beyond simple productivity improvement. It is also a process that, when done correctly, humanizes the workplace, eliminates overly hard work ("muri"), and teaches people how to perform experiments on their work using the scientific method and how to learn to spot and eliminate waste in business processes.
In all, the process suggests a humanized approach to workers and to increasing productivity: "The idea is to nurture the company's people as much as it is to praise and encourage participation in kaizen activities."
Successful implementation requires "the participation of workers in the improvement." People at all levels of an organization participate in kaizen, from the CEO down to janitorial staff, as well as external stakeholders when applicable.
JIT : TPS - SCM - CFM - DFM
Just-in-time (JIT) manufacturing, also known as just-in-time production or the Toyota production system (TPS), is a methodology aimed primarily at reducing flow times within production as well as response times from suppliers and to customers.
Alternative terms for JIT manufacturing have been used. Motorola's choice was short-cycle manufacturing (SCM). IBM's was continuous-flow manufacturing (CFM), and demand-flow manufacturing (DFM).
The Pareto principle (also known as the 80–20 rule, the law of the vital few, and the principle of factor sparsity) states that, for many events, roughly 80% of the effects come from 20% of the causes.
The distribution is claimed to appear in several different aspects relevant to entrepreneurs and business managers. For example:
-
80% of a company's profits come from 20% of its customers
-
80% of a company's complaints come from 20% of its customers
-
80% of a company's profits come from 20% of the time its staff spend
-
80% of a company's sales come from 20% of its products
-
80% of a company's sales are made by 20% of its sales staff
Therefore, many businesses have an easy access to dramatic improvements in profitability by focusing on the most effective areas and eliminating, ignoring, automating, delegating or retraining the rest, as appropriate.
Pareto Principle
KABAN
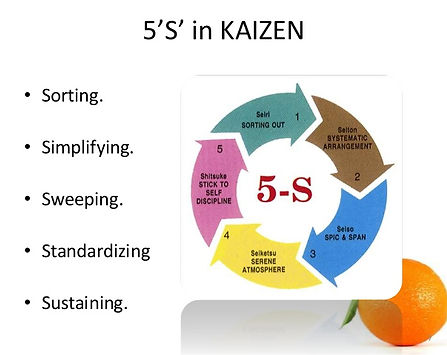
5 S
5S is the name of a workplace organization method that uses a list of five Japanese words: seiri, seiton, seiso, seiketsu, and shitsuke.
There are five 5S phases: They can be translated from the Japanese as "sort", "straighten", "shine", "standardise", and "sustain". Other translations are possible.
Seiri 整理 (Sort)
-
keeping only necessary items
-
Remove unnecessary items and dispose of them properly
-
Make work easier by eliminating obstacles.
-
Reduce chance of being disturbed with unnecessary items
-
Prevent accumulation of unnecessary items
-
Evaluate necessary items with regard to cost or other factors
-
Remove all parts not in use
-
Segregate unwanted material from the workplace
-
Need fully skilled supervisor for checking on regular basis
-
Don't put unnecessary items at the workplace & define a red-tagged area to keep those unnecessary items
Seiton 整頓 (Systematic Arrangement)
-
Can also be translated as "set in order", "straighten", or "streamline"
-
Arrange all necessary items so they can be easily selected for use
-
Prevent loss and waste of time
-
Make it easy to find and pick up necessary items
-
Ensure first-come-first-served basis
-
Make workflow smooth and easy
-
All above work should be done on regular basis
Seisou 清掃 (Shine)
-
Can also be translated as "sweep", "sanitize", or "scrub"
-
Clean your workplace completely
-
Use cleaning as inspection
-
Prevent machinery and equipment deterioration
-
Keep workplace safe and easy to work
-
Keep work place clean
Seikets 清潔 (Standardize)
-
Standardize the best practices in the work area.
-
Maintain high standards of housekeeping and workplace organization at all times.
-
Maintain orderliness. Maintain everything in order and according to its standard.
-
Everything in its right place.
-
Every process has a standard.
Shitsuke 躾 (Sustain)
-
To keep in working order
-
Also translates as "do without being told"
-
Perform regular audits
-
Training and Discipline
-
Training is goal oriented process. Its resulting feedback is necessary monthly
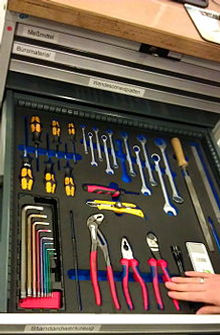